Nuestra 16ª Planta Compacta de Harina de Pescado CFP-60 ha sido entregada.
AMOF-Fjell Process Technology cuenta con una larga trayectoria en el diseño, fabricación, instalación y puesta en marcha de Plantas Compactas de Harina de Pescado para buques pesqueros.
Nuestra 16ª Planta Compacta de Harina de Pescado CFP-60 ha sido probada y entregada al cliente. La planta tiene una capacidad de 60 toneladas por día de materia prima residual (cabezas, recortes y vísceras) y producirá proteínas marinas y aceite de pescado de alta calidad.
El buque arrastrero ha sido diseñado por VARD (Design 8 04) y construido en Vard Vung Tau.
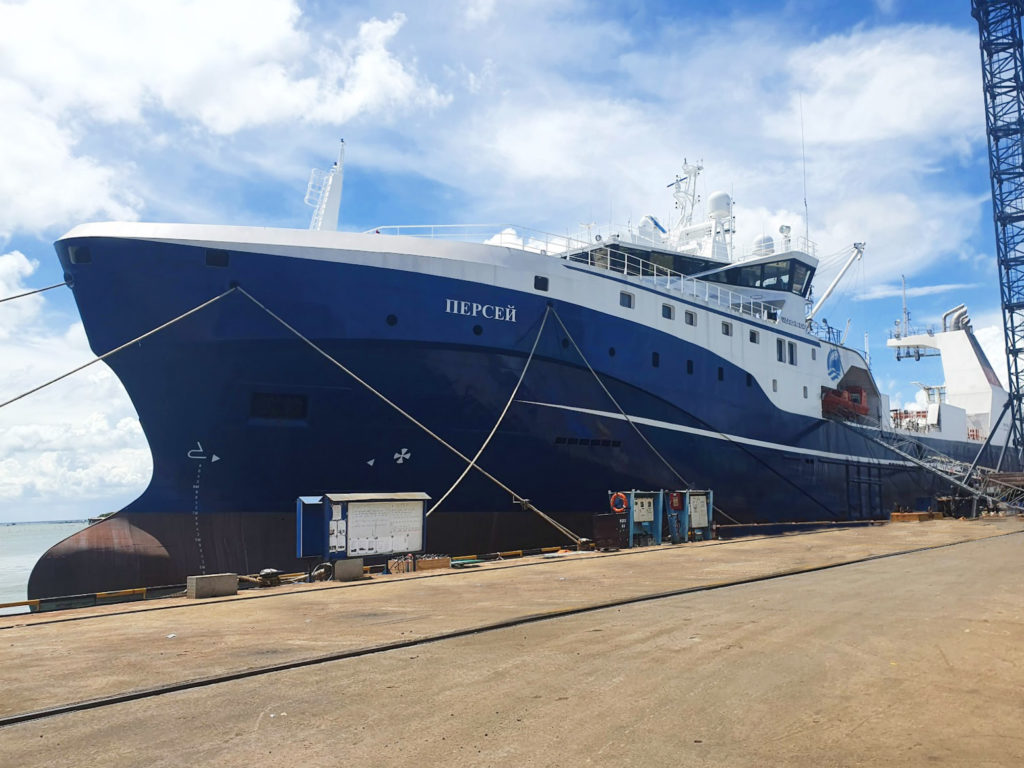
VARD (Design 8 04) y construido en Vard Vung Tau
AMOF-Fjell Compact Fishmeal Plant Para más información sobre Plantas Compactas de Harina de Pescado.
Descargar planilla:
AMOF-Fjell Compact Fishmeal Plants
Descripción funcional
- Los residuos de pescado deben ser pretratados de manera que se limite la cantidad de agua libre proveniente del procesamiento y transporte en la fábrica de pescado. Además, deben ser triturados en trozos gruesos para evitar cabezas y huesos grandes, sin ser reducidos a pulpa, antes de enviarse a la tolva de materia prima (el tanque de almacenamiento no incluido).
- Desde este tanque, el material es transportado mediante un transportador de tornillo o una bomba hacia la unidad de cocido.
- La unidad de cocido está diseñada como un gran transportador de tornillo de rotación lenta con una tubería exterior calentada por vapor y una hélice hueca también calentada por vapor. Esto permite calentar la materia prima a aproximadamente 90°C para garantizar su completa coagulación. Se recomienda un filtrado adicional del agua libre si se usa un transportador de tornillo.
- El material coagulado se dirige mediante uno o dos transportadores de tornillo (según el diseño final y la altura disponible) hacia la prensa de tornillo doble. Nuevamente, será necesario un filtrado adicional (en un transportador tamiz integrado o separado) para minimizar la cantidad de agua libre que llega a la prensa, ya que esto podría impedir un prensado completo.
- La prensa de doble tornillo consta de dos tornillos giratorios contrarrotantes con un ejes cónicos, de modo que el volumen comprendido entre los tornillos y la carcasa se reduce gradualmente. La carcasa está perforada para que se exprima el líquido y la torta de prensa se deposite o se transporte directamente al secador.
- El líquido resultante de la prensa se dirige al tanque de liquido prensado junto con los líquidos provenientes de los transportadores con colador y/o tamiz. Desde este tanque, el líquido se bombea al decantador de separación en 3 fases. En un solo paso, mediante fuerza centrífuga, separa la mezcla en una pulpa que contiene los sólidos suspendidos, agua con un alto contenido de proteínas solubles y aceite de pescado de alta calidad. La pulpa se transporta al secador, el agua con proteínas solubles se descarga al mar y el aceite se bombea a un tanque de almacenamiento adecuado.
- El secador consta de una chaqueta de vapor calefaccionada (opcional) y un rotor interno con discos huecos calentados con vapor. La mezcla de torta de prensa y pulpa del decantador de tres fases se calienta hasta el punto de ebullición, y el agua se evapora a medida que el material se transporta gradualmente hacia la salida del secador mediante agitadores instalados en la punta de los discos. La combinación de una rotación suave y la evaporación da como resultado harina de pescado con aproximadamente un 10 % de agua residual.
- El vapor de los secadores se extrae y se trata en un depurador de agua de mar junto con aire de ventilación y vapor de otros equipos del proceso (opcional).
- La harina de pescado cálida, con contenido de huesos y textura desigual se transporta mediante uno o dos transportadores a la planta de molienda.
- La planta de molienda convierte la harina en un polvo homogéneo.
- Después de la molienda, la harina se transporta al silo de harina, que sirve como el principal depósito para el envasado. El transporte puede realizarse mediante transportadores de tornillo enfriadores o un sistema neumático.
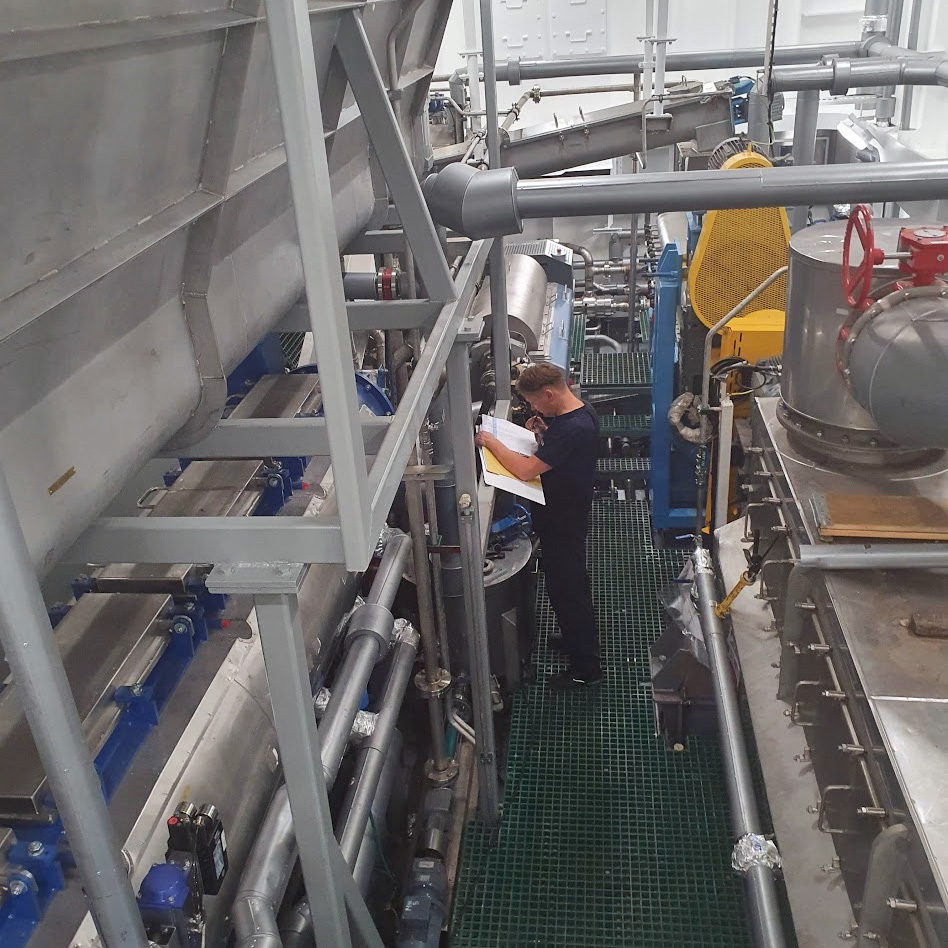